Durchführbarkeitsstudie zum Thermischen Beschichten von Bodenbearbeitungswerkzeugen
Aufgrund der vielfältigen Anwendungsmöglichkeit ist das thermische Spritzen sowohl in grundlegenden als auch in zukunftsweisenden Bereichen der Industrie ein etabliertes Beschichtungsverfahren. Entstanden aus dem Korrosions- und Verschleißschutz beispielsweise im Schiff- und Schienenbau, stehen heutzutage auch die funktionellen Schichteigenschaften wie z.B. Wärmdämmung, elektrische Leitfähigkeit sowie chemische Beständigkeit im Vordergrund der Verfahrensanwendung und -entwicklung. Zur Steigerung der Beanspruchbarkeit von Bauteilen und Werkzeugen, ist die Entwicklung individuell angepasster und hochleistungsfähiger thermisch gespritzter Schichten ein zentraler Entwicklungsschwerpunkt im Produktdesign und -refit.
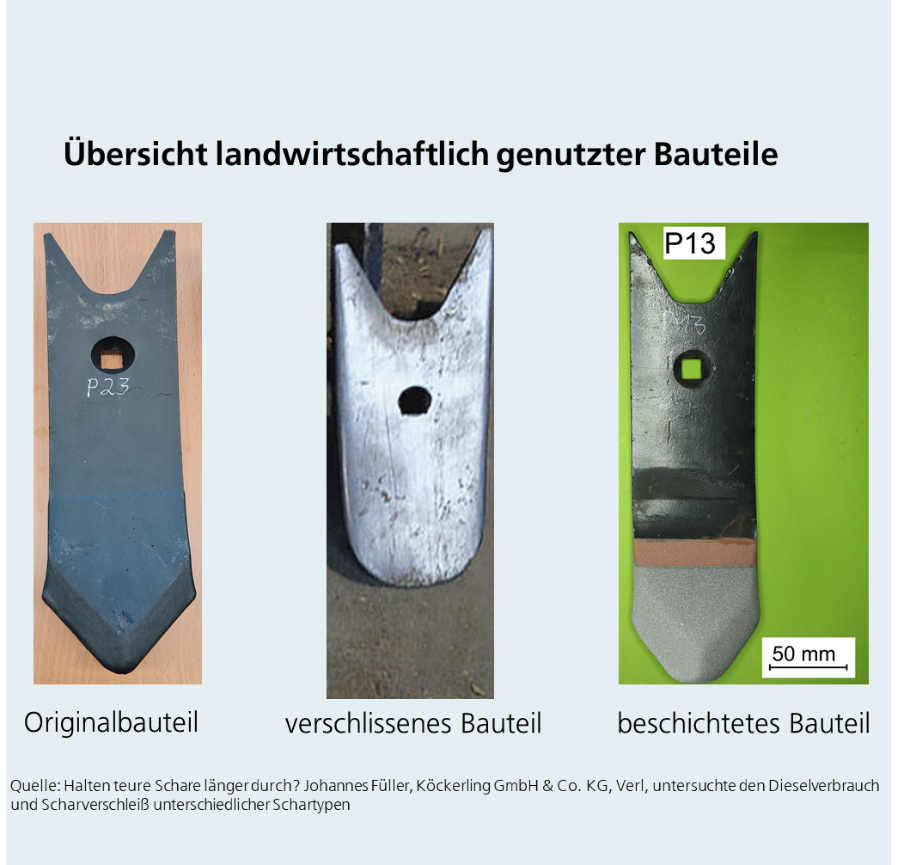
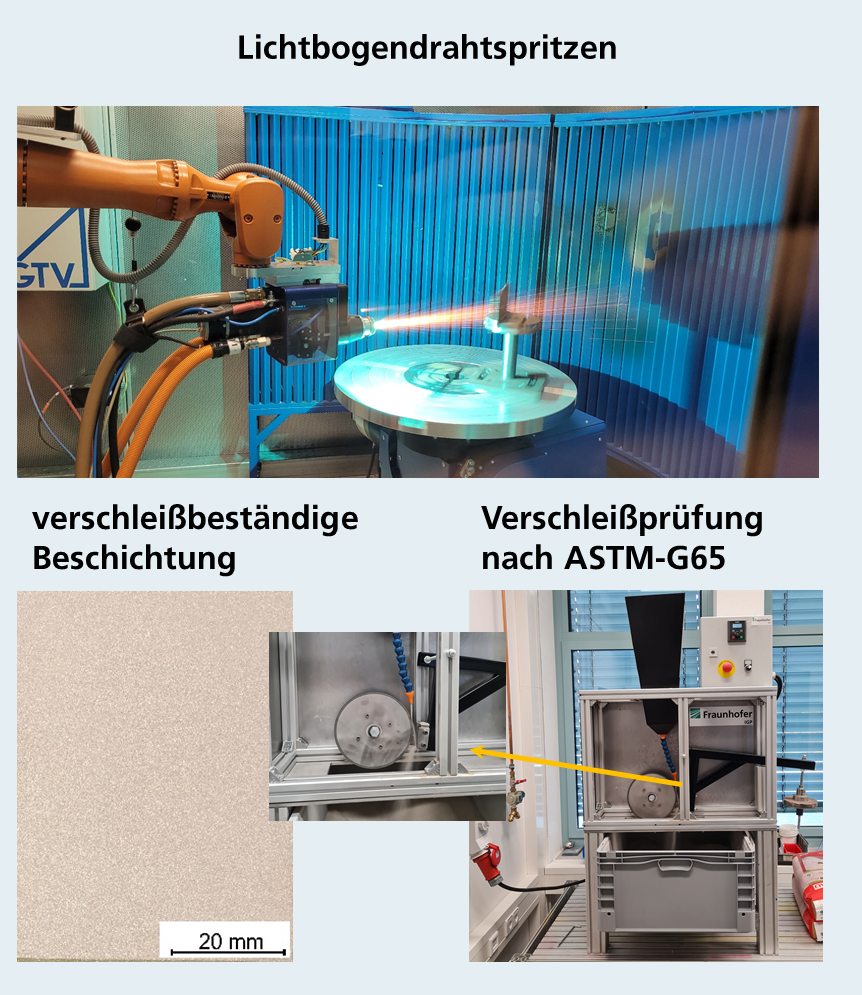
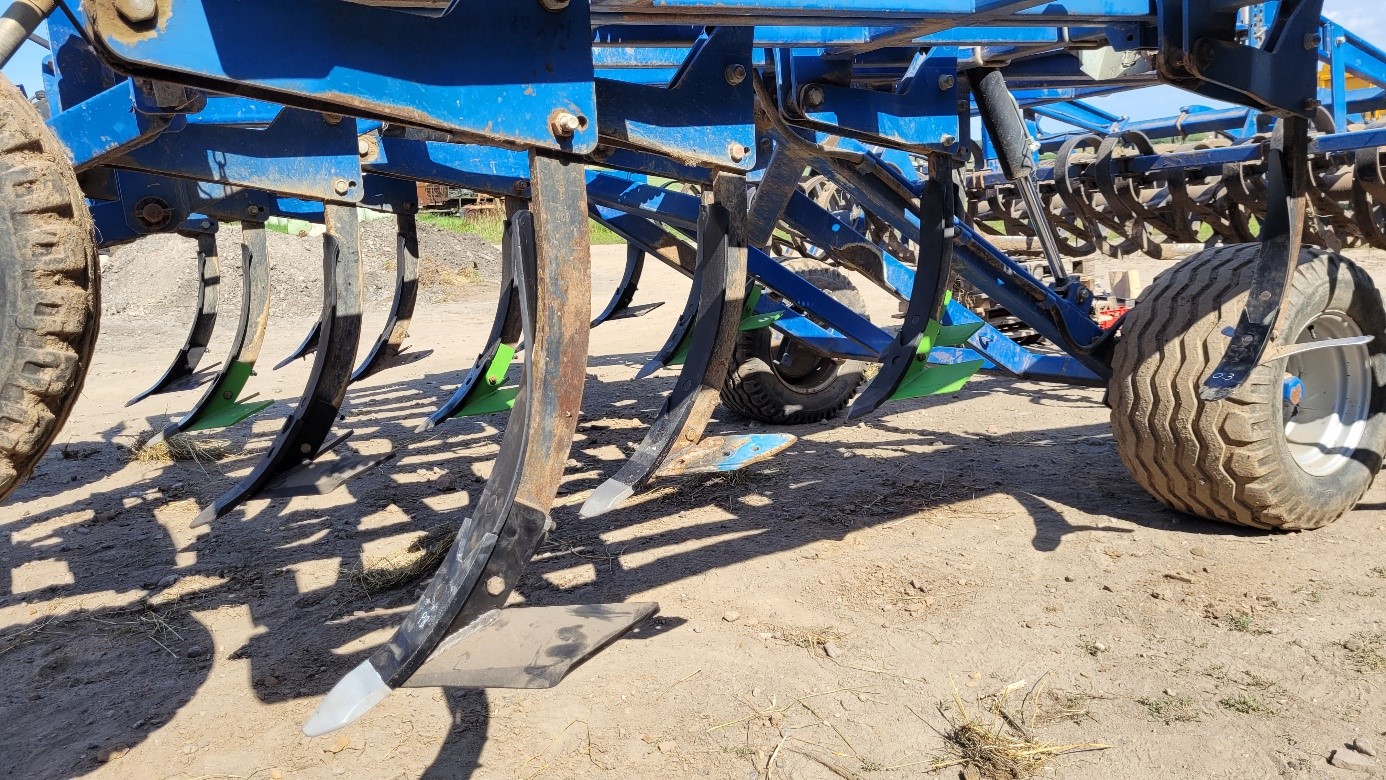
Problemstellung
Beim Einsatz von Bodenbearbeitungswerkzeugen in der Landwirtschaft steht die Widerstandsfähigkeit gegen Abrasionsverschleiß im Vordergrund. Da dieser je nach lokaler Bodenbeschaffenheit ungleichmäßig ist, ist der Verschleißfortschritt und somit der Zeitpunkt für den Werkzeugwechsel nur schwer zu identifizieren. Mögliche unerwünschte Folgen sind Bauteilversagen und -abbrüche sowie der unbekannte Bauteilverbleib im Feld mit potenzieller Schadensfolge für nachfolgende landwirtschaftliche Arbeitsgeräte. Hieraus resultiert neben einer verschleißfestigkeitssteigernden Beschichtung auch die Forderung nach einer Verschleißgrenzenanzeige, um so den Zeitpunkt für den Werkzeugwechsel genau bestimmen zu können.
Zielstellung und Lösungsweg
Ziel des Vorhabens ist die Entwicklung und Applikation eines Schichtsystems mit gesteigerter Verschleißbeständigkeit und integrierter optischer Verschleißanzeige. Zur Visualisierung der Verschleißgrenze soll eine Haftschicht auf Kupferbasis genutzt werden. Diese soll durch ihren markanten Farbunterschied zur Deckschicht, den Anwender die Verschleißgrenze aufzeigen. Desweitern ermöglicht dieser sogenannte Bondcoat eine bessere Anbindung der verschleißbeständigen Deckschicht an das Bauteil. Weiterhin soll durch die Flächenwirkung des Verfahrens die Wirtschaftlichkeit für die Beschichtung von verschleißbeständigen Bodenbearbeitungswerkzeugen gesteigert werden. Zum Beginn des Forschungsprojektes wurden zunächst die in der Praxis verwendeten Bauteile als Referenz im Verschleißprüfstand nach ASTM-G65 (Rubber-Wheel-Test) untersucht. Dieser Versuch ermöglicht die Quantifizierung und den Vergleich der Widerstandsfähigkeit von Bauteilen gegen Abrasion. Anschließend wurden geeignete Spritzverfahren sowie passende Zusatzwerkstoffkombinationen. Bezogen auf den Anwendungsfall, hat sich das Lichtbogendrahtspritzen mit verschleißbeständigen Fülldraht als beste Lösungsvariante herauskristallisiert. Da zum einen durch den verwendeten Zusatzwerkstoff die Einlagerung von Karbid-Hartphasen in das Schichtinterface ermöglicht werden kann und zum anderen die hohe Auftragsrate des Verfahrens eine hohe Wirtschaftlichkeit ermöglicht. Anschließend wurden die beschichteten Bauteile im Verschleißprüfstand sowie im Feldtest unter Realbedingung begleitenden von Projektpartnern untersucht und vergleichend gegenübergestellt.
Nutzen
Aufgrund der gewonnenen Erkenntnisse aus den zuvor erwähnten Untersuchungen, stellt das Lichtbogenspritzen im Vergleich zu etablierten Pulverbeschichtungen eine wirtschaftliche und verschleißsteigernde Alternative für die Anwendung an Bodenbearbeitungswerkzeuge in der Landwirtschaft dar. Des Weitern lassen sich durch die Flexibilität des Verfahrens anspruchsvolle Geometrien mit deutlich weniger Zeitaufwand beschichten. Dieser Vorteil wird vor allem bei großflächigen Bauteilen mit komplexen Bauformen wirksam, siehe Abbildung 1. Weiterhin bieten die thermisch beschichteten Bauteile dem Landwirt die Chance die verschlissenen Werkezeuge neu aufarbeiten zu lassen und so nachhaltig Kosten zu reduzieren und ressourcenschonend zu arbeiten. Nicht zuletzt kann in diesem Zusammenhang die verschleißanzeigende Schicht genutzt werden, um den entsprechenden Zeitpunkt für den Werkzeugwechsel zu signalisieren und so einen erhöhten Treibstoffverbrauch der Zugmaschine bzw. Totalversagen des Werkzeuges zu vermeiden.