Qualification of cast iron materials and thermal sprayed corrosion protection systems for underwater use under fatigue stress
Marine power plants represent a promising but currently underutilized option for supplementing established renewable energy generation options. German manufacturers in particular have developed various concepts and products in recent years, see Figure 1. Spheroidal graphite iron is often used for the construction of such systems. However, due to the direct contact of the fatigue-stressed components with seawater and conservative fatigue design regulations, some very unfavorable assumptions must be made in the design process, so that current concepts are associated with relatively high manufacturing costs.
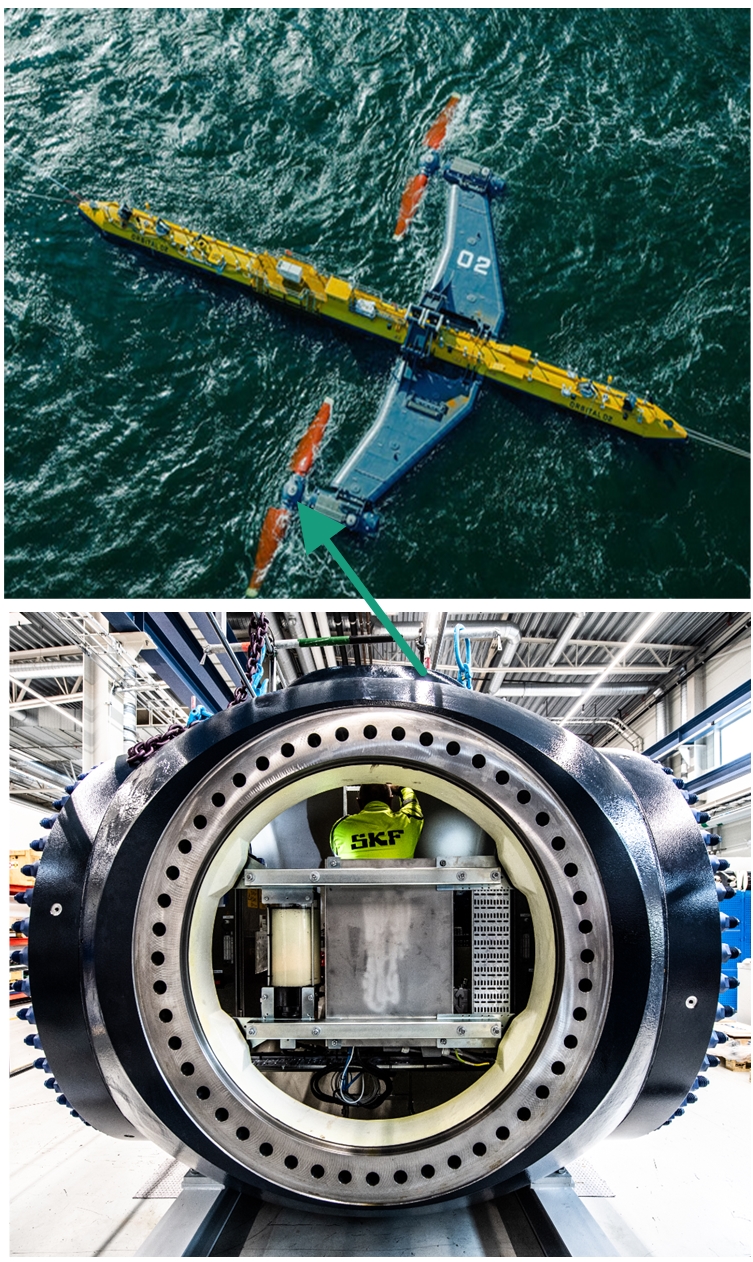
Problem
Due to good mechanical properties and comparatively low material costs, spheroidal graphite iron GJS-400 to GJS-600 is used in most components within the machine carriers, but also for highly dynamically stressed components such as blade bearings, hubs, bearing housings, front plates or propeller blades. Due to direct contact with seawater, the corresponding cast iron components are usually sealed with organic coatings and/or protected with sacrificial anodes. However, as these methods cannot always guarantee complete long-term corrosion protection, free corrosion of the components cannot be excluded. This must be taken into account in fatigue assessment, which often leads to uneconomical designs with high wall thicknesses and component weights.
Objective and solution
The aim of the project is to create a test-based approach for the design of spheroidal graphite iron in corrosive seawater environments under dynamic loading and to establish modern thermal coating technologies for long component lifetimes even under corrosive stress. Initial investigations indicate that the fatigue strength reduction prescribed by regulations is too conservative and that arc-sprayed coatings can also be applied to cast iron without having a significant negative impact on fatigue strength. Based on this, various typical thermally sprayed corrosion protection coatings, such as Al or Zn, are examined in the project with regard to their coating properties. Also, the effect of the coatings on the fatigue strength of correspondingly coated cast iron materials is investigated experimentally.
Benefit
By experimentally determining design values for fatigue-stressed cast iron materials under the influence of corrosion, components used under water can be more economically designed. If a sufficiently durable coating system can be established, users can take advantage of the new corrosion protection option to design parts and components with lower masses and, for example, offer marine power plants at lower costs. The findings on corrosion design and coating systems are also not limited to marine power plants. There is currently a lack of reliable data for the fatigue design of cast components used under water in all technical areas. Companies that apply thermal sprayed coating benefit from the project results, as do engineering firms that are responsible for component design. The participating foundries benefit from new areas of application for cast iron materials, which they can bring to the market and integrate into new product developments.